SMB Feldner are earning money while they sleep thanks to automated machine loading and unloading.
Loading and unloading machines
Special machine manufacturer SMB Feldner from Herzogenaurach specialises in the production of complex high-precision small series made of aluminium and steel. With its focus on complex high-precision workpieces, SMB Feldner has many orders that must be planned, designed and manufactured. Thomas Feldner can call on five skilled workers to equip eight tool milling machines and machining centres.
Although the design expertise is available, SMB Feldner has often had to turn down projects because the processing time in the tool milling machines and machining centres could not be implemented. Thanks to the robot solution for machine loading and unloading, Thomas Feldner was able to significantly increase machine capacity by using off-peak times. He realised the project together with the German robotics company coboworx, based in Rhineland-Palatinate and is currently accepting more orders as a result.
You can't even find an unqualified half-day worker for that price. In the black from the first month!
The challenge
SMB Feldner's greatest challenges are utilising the capacity of the expensive multi-axis machining centres and series production. If the milling machine is blocked while working on workpieces for a whole day or several days at a time, the production of individual parts suffers. Machining a more complex workpiece often takes 30 minutes or longer.
Series with 500 workpieces are relatively rare. Requests for small series with 5 to 10 workpieces are more common, but these have to be rejected as Thomas Feldner simply does not have the personnel to load and unload the machining centre every half hour. That's why he started looking for a flexible solution to automate the processing of very small series during night shifts or at weekends, so that the milling machine would be available again during the day for the production of individual parts.
For SMB Feldner, a collaborative robot supplying the 3-axis milling machine with workpieces was the ideal option. Besides the quick set-up, programming and changeover from one job to the next were the most important requirements for the operation. It was also desirable for the robot solution to be freely accessible, i.e. that it did not require a protective fence.
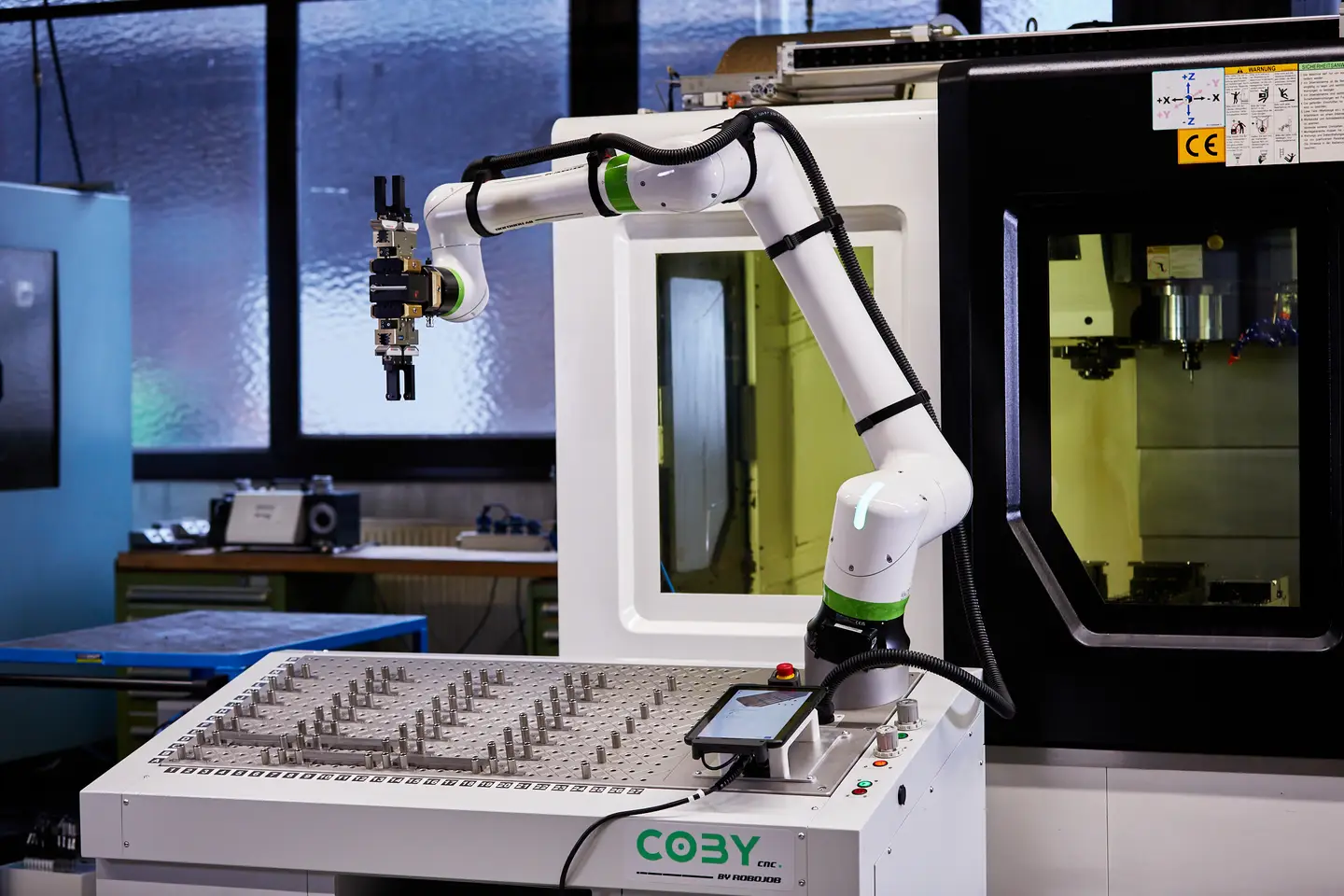
The search for the right robot solution
Thomas Feldner became aware of the robot solution for machine loading and unloading through an article about coboworx. After answering a few questions from the online configurator, he realised he was looking for one like this: a cobot solution that can be set up without expert knowledge, does not require a scanner or additional fencing, and is therefore fully accessible. He also found its flexibility a great advantage because a lift truck can easily reposition the compact robotic solution. This means that the most suitable machining centre can always be upgraded and its utilisation optimised.
Thomas Feldner is very open to innovations and is constantly looking for solutions that will take his production to the next level. "As Managing Director, I am always looking to improve how we work and invest in new technologies. Automation is an absolute must here," says Thomas Feldner.
The solution
The robot solution with a Fanuc Cobot enables an easy and rapid entry into automation without needing external technicians or training. It was specially developed for small and medium batch sizes and has a staging table for the workpieces to be processed of up to 5 kg, for which the Cobot is also ideally suited.
The solution is delivered compactly in a wooden box and fully assembled, positioned and set up on the relevant CNC machine. Familiarisation with the system and the one-off set-up usually takes less than a day, after which an employee can work independently with the robot solution.
The machine can be set up and retooled with workpieces via a guided program sequence within a few minutes. After the worker has defined the raw workpiece by entering its diameter and height, the deposit pattern is automatically generated, and the loading and unloading of the staging table is calculated. The operator knows immediately how to insert the pins into the table's grid system. The robot's path planning is also automatic. If the details of the raw piece are changed, the staging table's plug-in system can be reconfigured in a few simple steps.
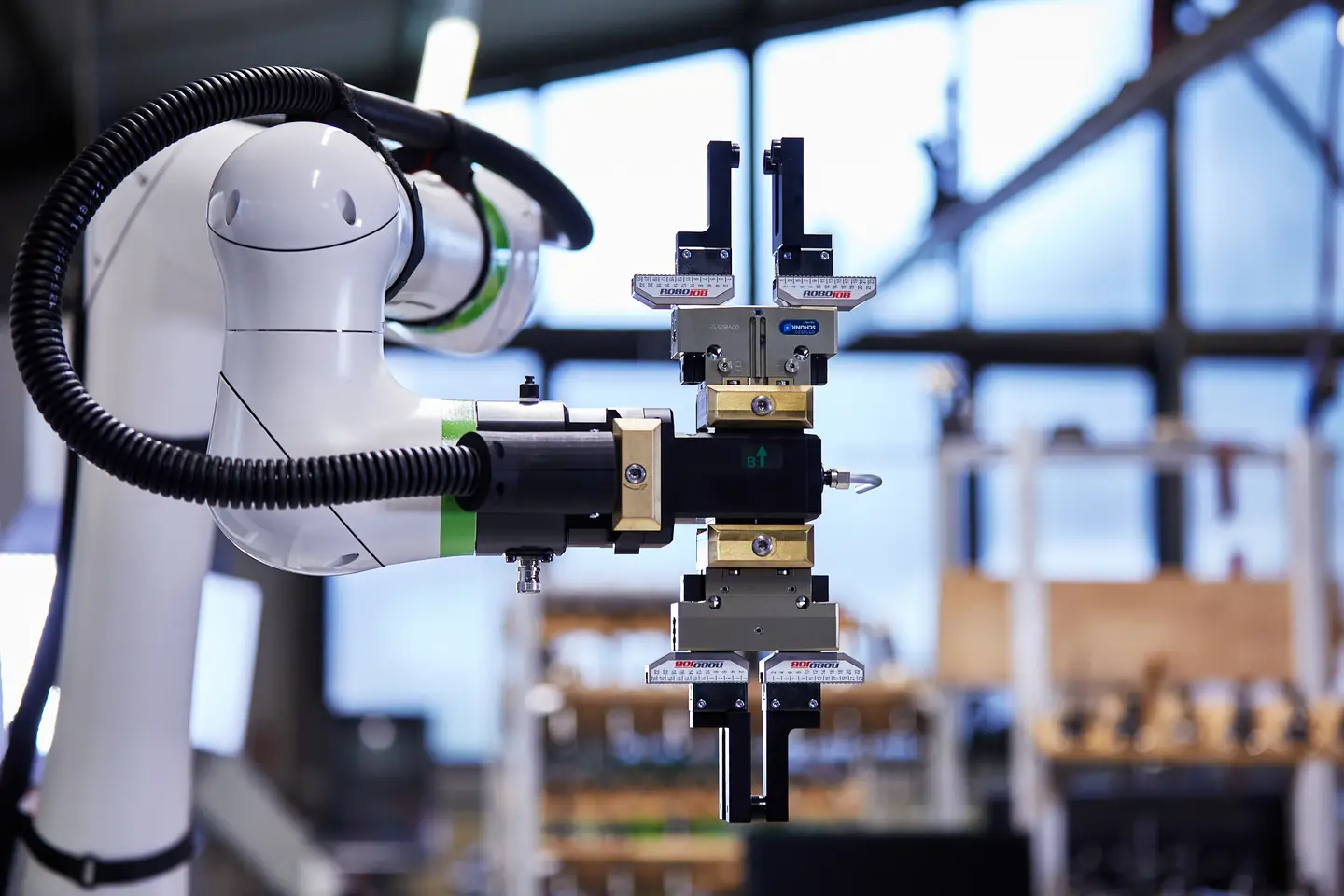
Most important features of the robot solution at a glance
- Collaborative robot system with a Fanuc CRX10iA
- Provision via a patented grid plate
- Space requirement of less than 1.5 m2
- Easy programming with no need for expert knowledge
- Just one day to set up the solution
- Including safety concept and CE certification
- Intuitive user interface
The robot solution is equipped with an exceptionally user-friendly and intuitive user interface, so no complex programming is necessary, and the robot solution can be put into operation without programming knowledge. This makes setting the solution up quick and straightforward. The clear interface makes calibrating and setting up the robot solution a breeze. Minimal technical knowledge of users is perfectly sufficient for commissioning.
The success – facts at a glance
- Space requirement of less than 1.5 m2
- Weight of workpieces – 5 kg
- Degree of automation – 85 per cent
- "Robots on subscription" monthly price – €2,080.00
With the robot solution for machine loading and unloading, Thomas Feldner can now accept orders that he previously had to turn down in some cases, as he can now also run the machine during nights and weekends. With the robot solution, SMB Feldner has increased the spindle-on time of its machining centres by more than 6 hours a day. The possibilities are still being exhausted, since the system could be further utilised at the weekend for larger batch sizes or longer machining times. Thomas Feldner is already looking forward to this, as he can now take on more and larger orders and "earn money in his sleep". The whole thing for €2,080 per month! "You can't even find an unqualified half-day worker for that price. In the black from the first month!", says Managing Director Thomas Feldner cheerfully. Now he can devote his time to producing individual parts during the day, while at night, the small series continue to run without employees in a blind shift.
"As a small manufacturer, I can now better compete with the larger companies in the area as I have gained a competitive advantage through automation. It is also obvious that it is becoming increasingly difficult to find skilled workers. Automation has made my staff's work easier and freed up time to prepare other machines and improve processes. This is a wonderful connection between my 3-axis milling machine and the robot solution," says Thomas Feldner.
All in all, automated machine loading and unloading brings SMB Feldner many advantages: It improves production efficiency and productivity as well as occupational safety, increases precision and consistency, offers flexibility in the design of production processes and saves costs in the long term.
Read about coboworx at their website or use the coboworx online-configurator.
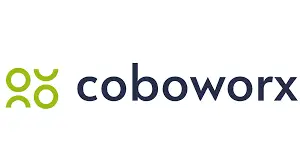